Contents
Raw Meal Beneficiation Learning Objectives
TO DOWNLOAD THE MOST IMPORTANT BOOKS , MANUALS , OPERATION NOTES , FORMUFLAS , EXCEL SHEETS CLICK HERE NOW !!
- Knowledge of the three major concepts in raw meal blending/homogenisation
- Knowledge of the basic concepts for kiln dust handling
- Knowledge of kiln feed concepts

Raw Meal Beneficiation Concepts

Silo Concepts
- Air-fluidized systems
- Aerated gravity systems
- Gravity systems
Air Fluidized Silo Systems
Batch type, two store arrangement

Air Fluidized Silo Systems: Aeration System

Air Fluidized Silo Systems :Operation
Performance Diagram of Batch Type Homogenizing Silo


Air-Fluidized Silo Concept: Valuation
+ Most efficient raw meal homogenizing system
– High energy consumer
– Application limited to about 2000t vessels,
thus sufficient for production lines up to 3000t/d
– High investment for new installations
Air Fluidized Silo Systems: Over-Flow System
CTS’ Vario-Flow System

Air Fluidized Silo Systems: Blending Efficiency



continuous homogenizing silo
Aerated Gravity Systems inverted cone concept
Design and operation concepts
- Spider on top of silo for meal distribution
- Inverted cone concept – empty cone (IBAU; K-P) – center chamber (BMH)
- One sector activated a time
- Aeration sequence as to minimize funnel intersection
- Single product discharge

Aerated Gravity Systems: Inverted Cone Silos

Blending Silos design + operation criteria
- No. of outlets: > D/2
- Cone/wall distance: < 2 m
- Max. air pad length: < 2.5 m
- Aeration air pad width: 200 mm
- Aerated bottom area: > 35 %
- Min. aeration air rate:
> 1 m3/min/m2
- Aeration sequence time: 6 – 12 min
- Aeration sequence
IBAU type blending silo

K-P tangential type blending silo
- No. of outlets: > D/2
- Cone/wall distance: < 2 m
- Max. air pad length: < 2.5 m
- Aeration air pad width: 200 mm
- Aerated bottom area:
> 35 %
- Min. aeration air rate:
> 1 m3/min/m2
- Aeration sequence time: 6 – 12 min
- Aeration sequence as for IBAU type

CPT type blending silo
- Cone/wall distance: < 2 m
- Max. air pad length: < 2.5 m
- Aeration air pad width: 200 mm
- Aerated bottom area:
35 – 50 %
- Min. aeration air rate:
1 – 2 m3/min/m2
- Aeration sequence time: 6 – 12 min
- Aeration sequence as for IBAU type

Blending Silos Multiple outlet silo

- No spider required on top of silo for meal distribution
- Flat bottom concept with multiple (7) outlets
- Product discharge at different rates from the outlets creating controlled declination of the layers
FLS-CF type blending silo

- Max. air pad length: < 2.5 m
- Aeration air pad width: 200 mm
- Aerated bottom area:
35 – 50 %
- Min. aeration air rate:
1 – 2 m3/min/m2
- Aeration sequence time: !!! strictly follow the operation manual !!!
Aerated Gravity Systems: Blending Behavior

Aerated Gravity Systems: Validation
+Applicable for wide capacity ranges (5’000 – 20’000t)
+Low energy consumer
-Limited beneficiation potential 5:1
-Decreasing beneficiation potential with increasing raw meal uniformity ex raw mill
-Insufficient reduction of
– long term fluctuations
– peak and step type disturbances
Homogenizing versus Blending

Gravity Systems: The Multi-Pack System
7+1-Pack-Silo: Operation Mode
- Separate chamber for kiln dust handling
- Subsequent filling of silo cells
- Simultaneous reclaim from all cells

Raw Meal Preparation
Raw Meal Preparation Performance Indicators
- Residual moisture raw meal:target value: £ 0.5 [%]
- Uniform fineness (CoV: R 90 µm): target value: £ 5 [%]
- Uniformity of kiln feed (standard deviation sLSF) target value: £ 1.2 [ – ]
- Silo blending efficiency

Raw Meal Preparation Uniformity Goals
- Characteristics for product uniformity and goals for excellence

Raw Meal Preparation Benchmarks

Raw Mix Preparation Uniformity Goals

Reasons for Insufficient Raw Meal Uniformity
- Bad condition of silo (e.g. water ingress)
- Malfunction of the silo system
- Non-uniform raw meal distribution
- Inadequate aeration sequence
- Inadequate filling degree
- Insufficient aeration time (batch type silo)
- Inadequate raw mix preparation
- Inadequate kiln dust handling
- Inadequate feed rate control to kiln
Impacts on Kiln Feed Uniformity
- Operation of the homogenizing/blending silo
- The method of dust handling
- The equipment available for kiln feed proportioning
Continuous Blending Silos: Problems

Aeration Air Problems with Distribution

Improve air distribution by the installation of solenoid valves replacing mechanically delicate air distributors
Continuous Blending Silos Measures
- Operate the silos at high filling levels (> 75 %)
- Activate single sectors at a time rather than two opposite sectors
- Select optimum sector activation sequence preventing intersection of funnels at material surface

Continuous Blending Silos: Problems
Continuous blending silos can hardly deal with long term compositional fluctuations

Continuous blending silos can hardly deal with peak/step type compositional fluctuations
Addition of kiln dust into a blending silo may be a reason for such peak type fluctuation !!!

Effect of Inadequate Raw Mix Preparation on Raw Meal Uniformity
Effect of Inadequate Raw Mix Preparation on Raw Meal Uniformity
Kiln Dust Handling
Kiln dust Handling Testing the Separation Factor
Testing the separation factor as a measure to judge a raw meal’s tendency to segregation
- sampling of raw meal ex raw mill
- chemical analysis of total sample: main elements LSF
- split sample into sub-samples: < 32 mm fraction 32 – 90 mm fraction > 90 mm fraction
- chemical analysis of sub-samples: main elements LSF
- calculate separation factor (SF): LSF<32mm/LSFtot
Þ range of not critical raw meals: 0.8 < SF < 1.2
Kiln Dust Handling Problem 3: Concepts
compound operation mode
- Kiln dust/raw meal mix fed into blending silo
direct operation mode
- Kiln dust added into blending silo
- Kiln dust addition into kiln feed bin, by-passing the blending silo
- Diluted kiln dust added into blending silo
- Kiln dust addition to kiln feed bin out of separate kiln dust bin
- Kiln dust discharge to separate kiln dust bin and continuous proportioning to cement
Kiln Dust Handling By-Pass to Meal Silo
Evaluation:
+ standard arrangement simple, inexpensive
– compositional step type variations when starting/stopping the raw mill
– compositional variations may become excessive with out-of-range meal qualities (0.8 < SF < 1.2)
Applications: many

Kiln Dust Handling Dilution of Kiln Dust
Evaluation:
+ simple arrangement
– gradually changing composition of the raw meal stock on hold in the silo when stopping the raw mill
– additional silo outlet
– compositional variations may become excessive with out-of-range meal qualities (0.8 < SF < 1.2)
Applications: SCL, Chekka

Kiln Dust Handling Separate Kiln Dust Bin
Evaluation:
+ narrow range for compositional kiln feed variations
– expensive solution
Applications: Holnam, Holly Hill project

Kiln Dust Handling Proportioning to Cement

Evaluation:
+ valve for kiln dust enriched with Cl and/or S
(Separate) Kiln Dust Bin Design Concept

Kiln dust bin
- sizing: acc. spec. requirements
- installation: on load cells
- product activation: by aeration or mechanical
Rate control
- feeder: – Rotor Scale – Coriolis type flow meter
Transport
- feed point: to raw meal at inlet of kiln feed bin
Kiln Feed Proportioning
Kiln Feed Proportioning Demands
- consistent raw meal reclaim from feed bin
- permanent gravimetric rate control
- high feed rate accuracy for a wide control range
-short term: better than ± 1.0 % ref to 10 s measurements
-long term: better than ± 0.5 % referring to set point
- sensitivity to set point adjustments: better than ± 0.5 %
- consistent raw meal transport to the kiln
- high operation reliability
- fully enclosed design
- low maintenance requirements
Kiln Feed Proportioning: Bin Design and Operation

- Sizing: for at least 15 min of kiln operation
- Installation: on load cells
- Operation: at constant level (70 – 80 % filling)
- Feed rate control out of blending silo: by flow control gate
Kiln Feed Bin Design and Operation
- Sizing: for at least 15 min of kiln operation
- Installation: on load cells
- Operation: at constant level (70 – 80 % filling)
- Feed rate control by flow control out of blending silo: gate
Feeder Selection
Feeder Survey (1)
![Rotor Scale Coriolis Poldos control concept gravimetric volumetric volumetric feed rates [t/h] up to 500 up to 210 up to 450 accuracy long term better than 0.5% better than 0.5% better than 1.0% accuracy short term better than 1.0% better than 1.0% better than 2.0% sensitivity to adjustments better than 0.5% better than 0.5% better than 1.0% sensitivity to external effects low low medium system design closed closed closed maintenance low low low](https://sp-ao.shortpixel.ai/client/to_auto,q_lossless,ret_img,w_571,h_380/https://www.cementequipment.org/wp-content/uploads/2016/09/Feeder-Survey-1.png)
control concept gravimetric volumetric volumetric
feed rates [t/h] up to 500 up to 210 up to 450
accuracy
long term better than
0.5% better than
0.5% better than
1.0%
accuracy
short term better than
1.0% better than
1.0% better than
2.0%
sensitivity
to adjustments better than
0.5% better than
0.5% better than
1.0%
sensitivity
to external effects low low medium
system design closed closed closed
maintenance low low low
Feeder Survey (2)
![Impact Flow Meter Weigh Feeder Air-lift System L-i-W System control concept volumetric gravimetric volumetric volumetric feed rates [t/h] up to 1000 up to 350 up to 500 up to1000 accuracy long term 2.0% 1.0% 2.0% 2.0% accuracy short term at best 2.0% 2.0% at best 2.0% worse than 2.0% sensitivity to adjustments low 1.0% at best 1.0% low sensitivity to external effects high high low high system design closed open closed closed maintenance low high low high](https://sp-ao.shortpixel.ai/client/to_auto,q_lossless,ret_img,w_598,h_365/https://www.cementequipment.org/wp-content/uploads/2016/09/Feeder-Survey-2.png)
System
control concept volumetric gravimetric volumetric volumetric
feed rates [t/h] up to 1000 up to 350 up to 500 up to1000
accuracy
long term 2.0% 1.0% 2.0% 2.0%
accuracy
short term at best
2.0% 2.0% at best
2.0% worse than 2.0%
sensitivity
to adjustments low 1.0% at best
1.0% low
sensitivity to external effects high high low high
system design closed open closed closed
maintenance low high low high
Feeder Selection Conclusion
First choice
- Pfister
Rotor Scale - Schenck
Coriolis type flow meter - Polysius
POLDOS SR system
Second choice
- impact flow meter
- weigh feeder
- air-lift systems
- loss-in weight systems
Applications
Rotor Scales
- Holcim (US), Devil’s Slide
SRW1.18 175 t/h - Cementos Progresso
FRW 2.2 270 t/h - Holcim (Costa Rica), Cartago
FRW 2.14 74 t/h - Holcim (Maroc), Oujda
FRW 3.14 200 t/h - Holdercim, Pedro Leopoldo
FRW 3.20 400 t/h
Coriolis Type Flow Meter
- China Cement Hongkong 1999
(Green Island Cement)
MULTICOR S300 2 x 210 t/h
(installed above preheater)

POLDOS SR
- Apasco, Orizaba 160 t/h
- Holcim (Liban), Chekka 440 t/h
- Holcim (US), Holy Hill project 495 t/h
- SLC, Greenport project 495 t/h
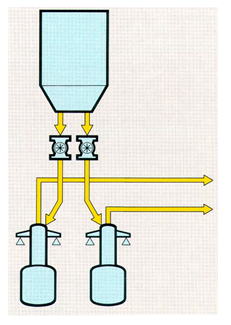
System Arrangement
at Ground Level
standard solution
+ no automatic sample transport
+ access for sampler maintenance
+ meal recirculation via second silo outlet
+ kiln dust dilution possible via second silo outlet
+/- silo not elevated but additional structure
– additional bucket elevator
– high kiln feed bucket elevator
– long reaction time for set point adjustments
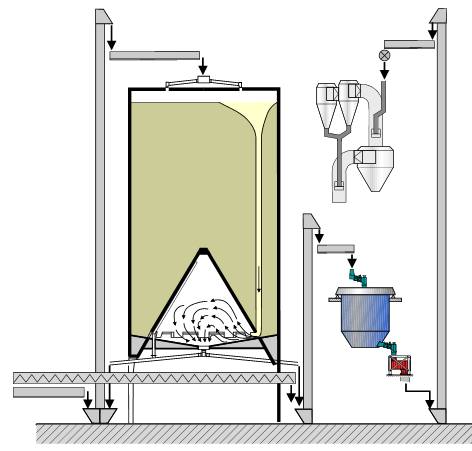
below elevated Silo
standard solution
+ no additional bucket elevator
+ easy meal recirculation via second silo outlet
+ no automatic sample transport
+ access for sampler maintenance
+ kiln dust dilution possible via second silo outlet
+/- no additional structure but elevated silo
– high kiln feed bucket elevator
– long reaction time for feed rate adjustments

on roof of Meal Silo
Application: Apasco, RA2 project
+ reduced reaction time on feed rate adjustments
+ no additional structure
+ no additional bucket elevator
+ reduced height of kiln feed bucket elevators (two stages)
+ easy meal recirculation
+ kiln dust dilution possible via second silo outlet
– automatic sample transport
– access for sampler maintenance

at Top of Preheater
Application: Apasco, AP mod
++ short reaction time on feed rate adjustments
+ easy meal recirculation via second silo outlet
+ kiln dust dilution possible via second silo outlet
+/- no additional structure but additional space requirement and loads for preheater structure
– automatic sample transport
– access for sampler maintenance

The Raw Meal Preparation Sequence

if you have any questions
please contact us at : project20062015@gmail.com
https://www.facebook.com/cementequipment.org
TO DOWNLOAD THE MOST IMPORTANT BOOKS , MANUALS , OPERATION NOTES , FORMUFLAS , EXCEL SHEETS CLICK HERE NOW !!
Hey there! I could have sworn I’ve been to this website before but after browsing through some of the post I realized it’s new to me. Nonetheless, I’m definitely delighted I found it and I’ll be bookmarking and checking back often!
I simply want to tell you that I’m newbie and really liked your web page. More than likely I’m want to bookmark your blog post . You certainly come with great posts. Kudos for sharing your web-site.
Good information, you could give some reference about separation factor?
Thanks